Hydraulic and pneumatic systems are widely used across various industries, but each has its own set of advantages and limitations that make it more suitable for specific tasks. The key differences between the systems go beyond their basic components—they extend to factors like force, speed, precision, environmental impact, and overall cost. Understanding these differences is essential for engineers and designers to make an informed decision that aligns with their operational needs. This article will delve deeper into the key differences between both systems.
Understanding Hydraulic Systems
Hydraulic systems rely on incompressible liquids, typically oil, to transmit power. These systems are known for their high power density and precise control, making them ideal for heavy-duty applications.
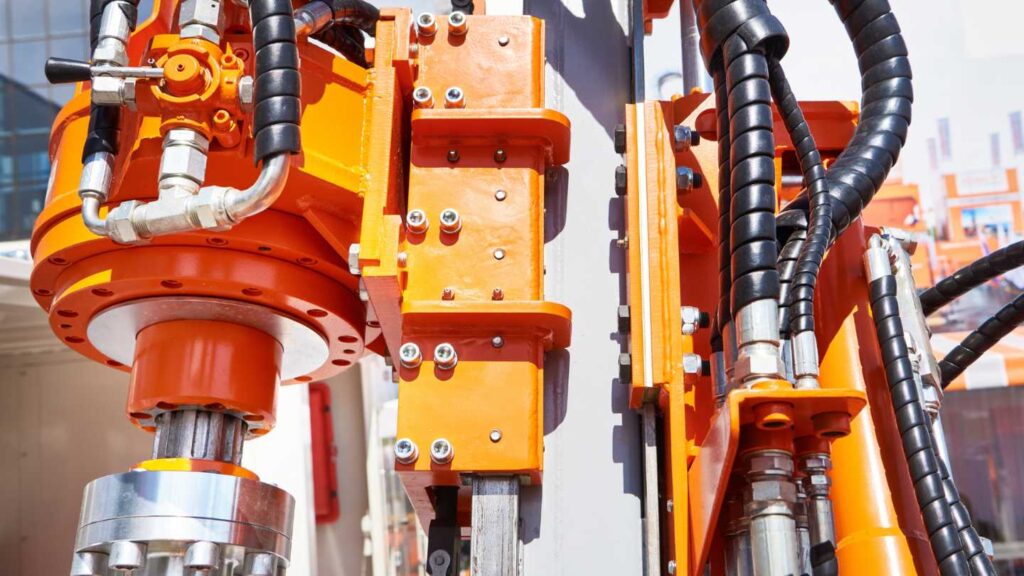
Key Components:
- Hydraulic Pump: Converts mechanical energy into hydraulic energy.
- Valves: Control the flow and pressure of the fluid.
- Actuators: Convert hydraulic energy into mechanical motion (linear or rotary).
- Reservoir: Stores the hydraulic fluid.
- Pipes and Hoses: Transport the fluid within the system.
Understanding Pneumatic Systems
Pneumatic systems use compressed air or gas to transmit power. They are lightweight, cost-effective, and clean, making them suitable for applications requiring moderate force.
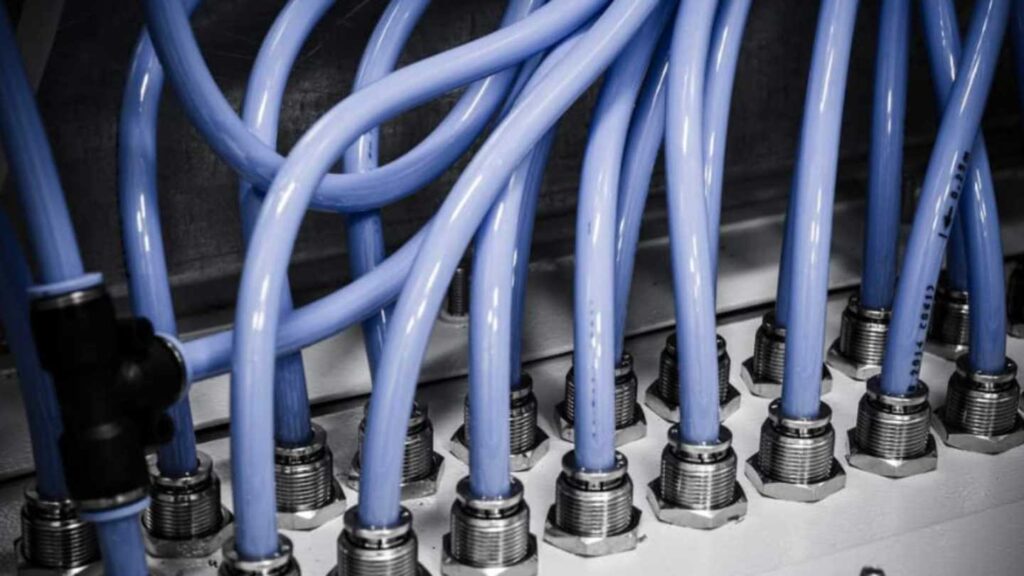
Key Components:
- Compressor: Generates and compresses air.
- Valves: Regulate air flow and direction.
- Actuators: Convert air pressure into mechanical motion.
- Air Treatment Units: Ensure air is clean and moisture-free.
- Pipes and Fittings: Distribute compressed air to the system.
Key Differences Between Hydraulic and Pneumatic Systems
The table below highlights the primary differences between the two systems:
Feature | Hydraulic Systems | Pneumatic Systems |
Medium | Incompressible fluid (oil or water-based). | Compressed air or gas. |
Pressure Range | High (up to 10,000 psi or more). | Low to moderate (up to 150 psi). |
Power Density | High – suitable for heavy-duty tasks. | Lower – ideal for lighter tasks. |
Precision | High – enables precise control. | Moderate – less precise than hydraulics. |
Speed | Generally slower. | Faster due to air compressibility. |
Maintenance | Requires regular checks for leaks and fluid quality. | Relatively low maintenance. |
Initial Cost | Higher due to complex components. | Lower initial investment. |
Applications | Heavy machinery, construction, and aviation. | Packaging, assembly, and lightweight tools. |
Applications
Both systems have distinct application areas based on their operational characteristics.
Hydraulic Systems Applications
- Construction Equipment: Excavators, bulldozers, and cranes rely on hydraulic power for heavy lifting and digging.
- Aviation: Aircraft control systems use hydraulics for landing gear, brakes, and wing flaps.
- Manufacturing: Hydraulic presses, injection molding machines, and metal forming equipment.
- Automotive: Hydraulic brakes and power steering systems.
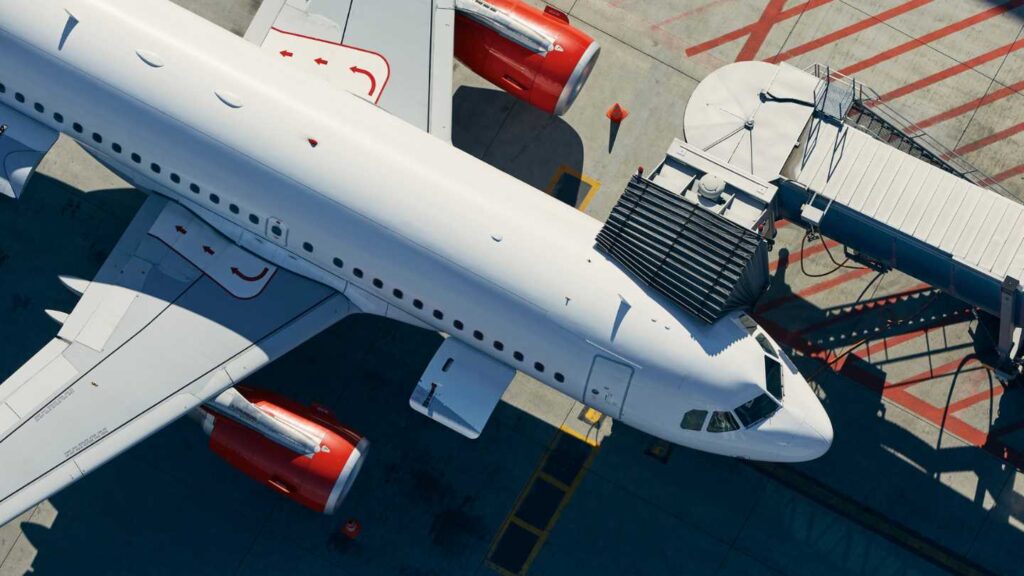
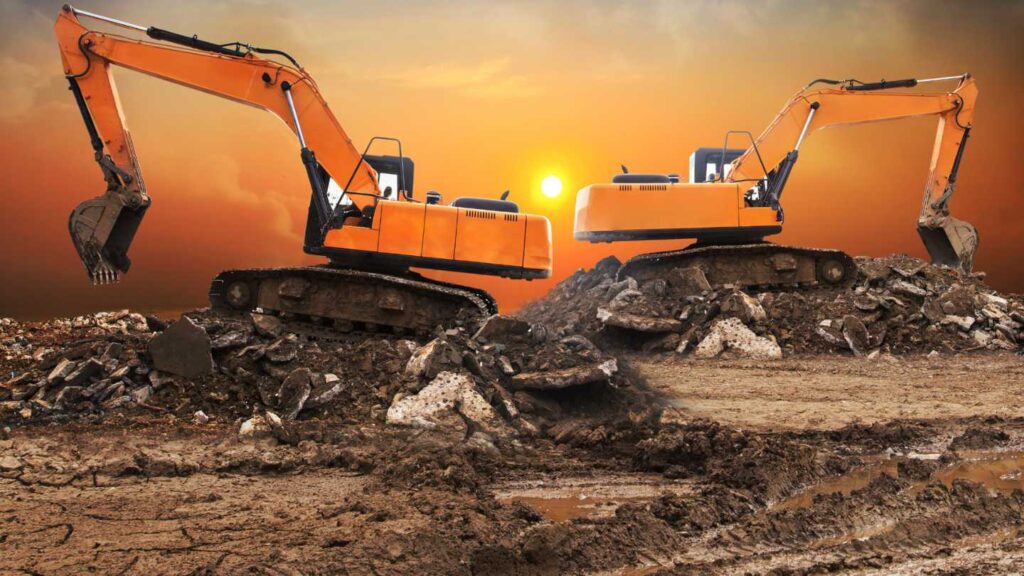
Pneumatic Systems Applications
- Packaging Industry: Pneumatic conveyors and packing machines operate efficiently with compressed air.
- Automated Assembly Lines: Lightweight pneumatic tools provide precision and speed.
- Medical Devices: Dental drills and patient lift systems use pneumatic power for safety and cleanliness.
- Transportation: Pneumatic brakes in trains and buses ensure reliable stopping power.
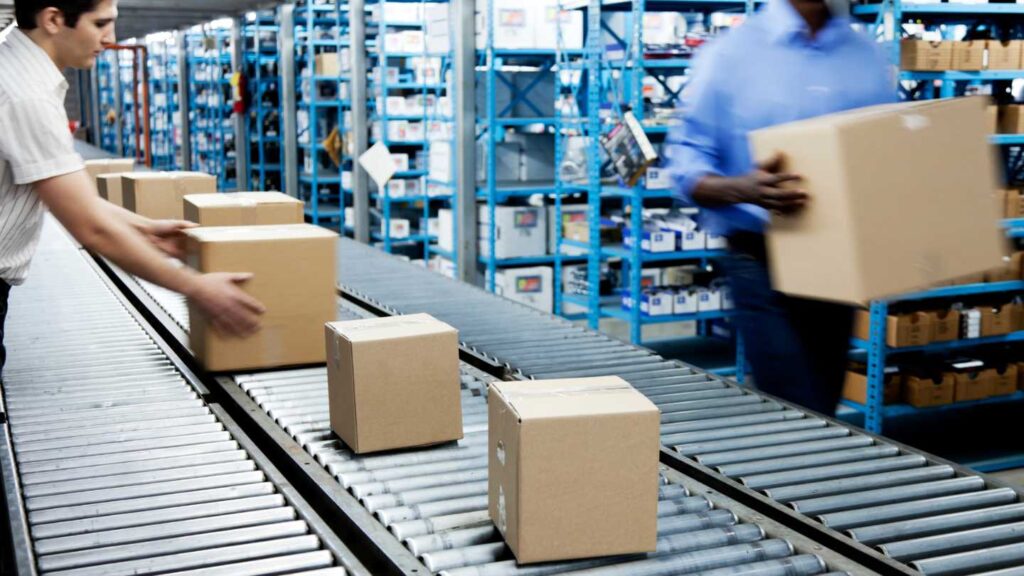
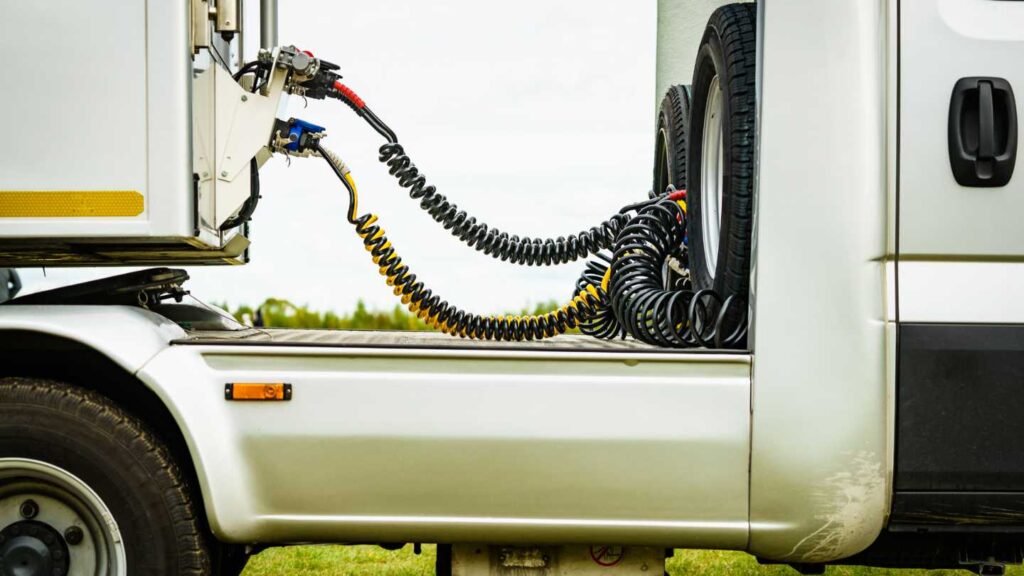
Choosing Between Hydraulic and Pneumatic Systems
When deciding between both systems, consider the following factors:
- Force Requirements: Use hydraulics for high force and precision. Pneumatics are better for light to moderate tasks.
- Speed Needs: If speed is critical, pneumatic systems are more suitable.
- Cost Constraints: Pneumatic systems generally have a lower initial cost but may have higher operational expenses due to energy usage.
- Environmental Considerations: Pneumatics are cleaner and safer for environmentally sensitive areas.
Conclusion
Both pneumatic and hydraulic systems play crucial roles in modern industries. The choice between the two depends on specific application requirements, including force, speed, precision, and cost. By understanding the key differences and advantages of each, businesses can make informed decisions to optimise performance and efficiency.
For more insights or to explore high-quality solutions, visit CT Hydraulics. Our experts are ready to assist with tailored advice for your industrial needs.