Hydraulic fluid testing is essential for the performance and longevity of many industrial and mechanical applications, from manufacturing plants to construction equipment. These systems rely heavily on hydraulic fluid to transmit power efficiently. However, like any other critical component, hydraulic fluid requires regular testing and maintenance to ensure optimal performance and system longevity. Neglecting this essential task can lead to equipment failure, costly repairs, and significant operational downtime.
In this blog, we’ll explore why regular hydraulic fluid testing is crucial, the benefits it provides, and what parameters should be monitored to maintain a reliable and efficient system.
Why is Regular Hydraulic Fluid Testing Important?
Hydraulic fluid performs multiple critical functions, including power transmission, lubrication, heat dissipation, and contamination control. Over time, this fluid can degrade due to contamination, oxidation, and water ingress. Regular testing helps identify these issues early, preventing potential damage and ensuring the system operates smoothly.
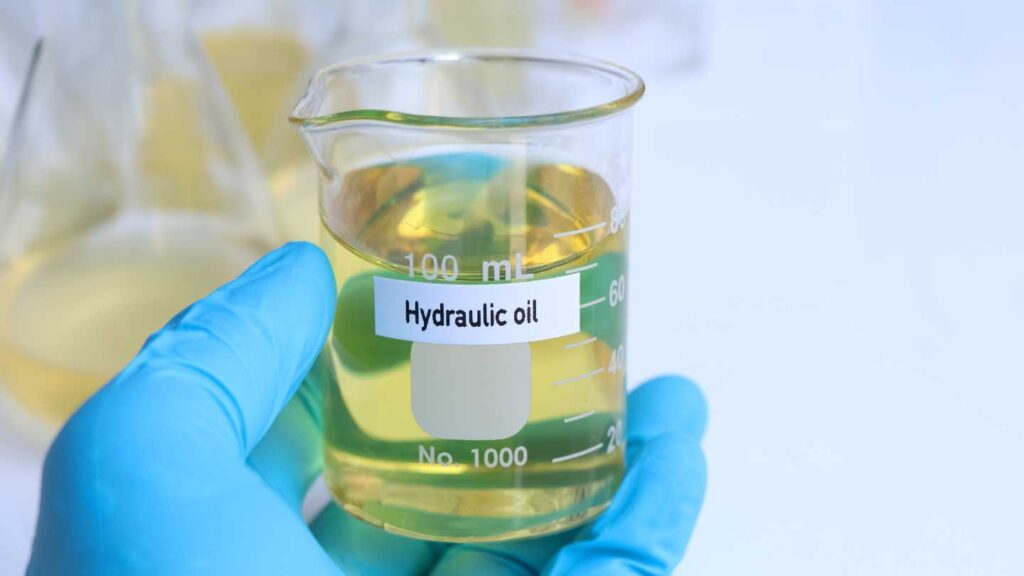
Key Reasons for Regular Hydraulic Fluid Testing:
- Prevent Equipment Failure: Contaminated or degraded fluid can lead to component wear, overheating, and potential equipment breakdowns.
- Ensure Optimal Performance: Clean and healthy hydraulic fluid maintains consistent system performance.
- Reduce Maintenance Costs: Early detection of fluid issues can prevent costly repairs or part replacements.
- Extend Equipment Lifespan: Regular testing and maintenance help prolong the life of hydraulic components.
- Ensure Safety and Compliance: Some industries have strict regulations regarding hydraulic system maintenance for safety and environmental reasons.
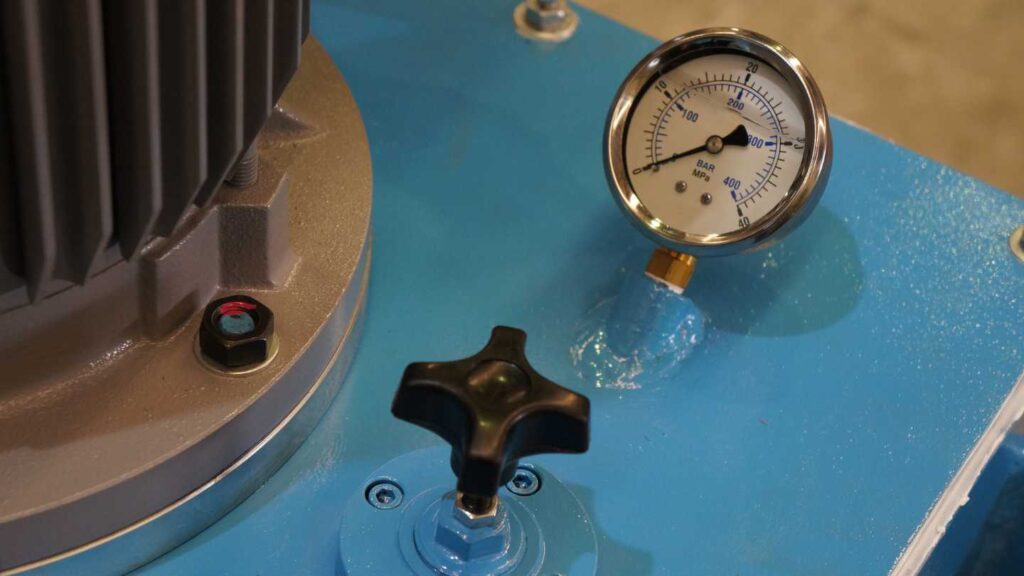
What Parameters Should Be Tested?
When conducting hydraulic fluid testing, several key parameters should be assessed to evaluate the fluid’s health and performance. The table below provides an overview of these critical parameters and their significance.
Parameter | Description | Significance |
Viscosity | Measure of fluid thickness and resistance to flow | Ensures proper lubrication and efficiency |
Water Content | Presence of water in the fluid | Prevents corrosion and component damage |
Particle Contamination | Measures particulate matter (ISO cleanliness codes) | Prevents abrasion and wear |
Acid Number (AN) | Indicates fluid acidity due to oxidation | Protects against corrosion and degradation |
Oxidation Stability | Measures resistance to oxidation | Extends fluid life and performance |
Additive Depletion | Evaluate the levels of protective additives | Ensures continued fluid effectiveness |
Best Practices for Hydraulic Fluid Testing
To maximize the benefits of hydraulic fluid testing, it’s essential to follow the best practices:
- Establish a Testing Schedule: Implement a routine testing program based on system usage, manufacturer recommendations, and environmental conditions.
- Use Accredited Laboratories: Partner with reputable testing services equipped with advanced diagnostic tools.
- Document and Analyse Trends: Maintain records of test results to track fluid condition trends and predict potential issues.
- Act on Test Results: Promptly address any irregularities identified during testing to avoid further damage.
- Train Personnel: Ensure maintenance staff are trained in proper sampling techniques to avoid sample contamination.
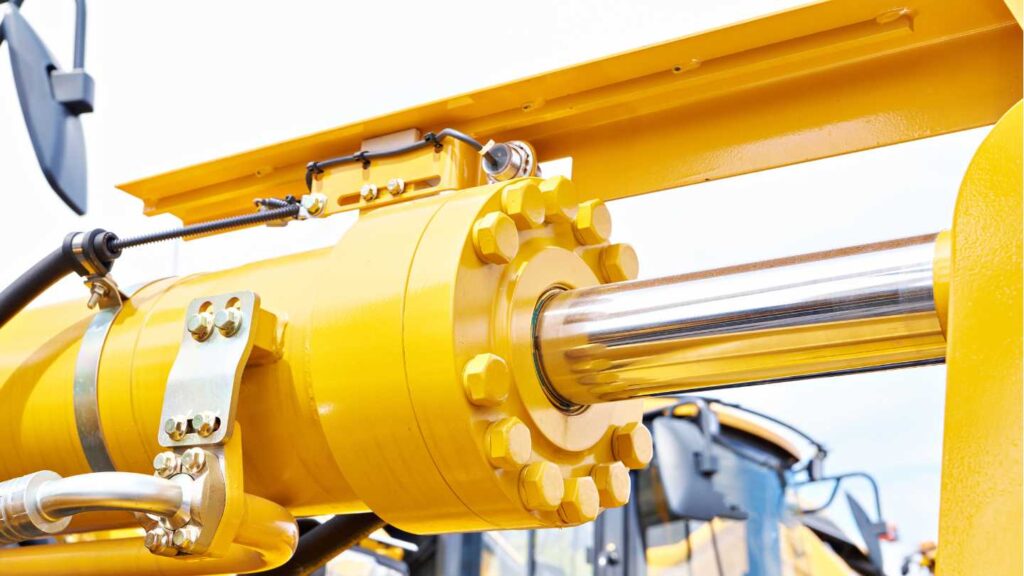
The Cost of Neglecting Hydraulic Fluid Testing
Ignoring regular hydraulic fluid testing can result in severe operational and financial consequences. Contaminants such as water, dirt, and metal particles can accelerate component wear, leading to expensive repairs or replacements. Additionally, unplanned downtime can disrupt production schedules, affecting overall productivity and profitability.
Consider the following potential costs of neglect:
- Increased component wear and tear
- Unplanned equipment failures and downtime
- Higher energy consumption due to reduced efficiency
- Regulatory non-compliance and potential fines
- Safety hazards for operators and nearby personnel
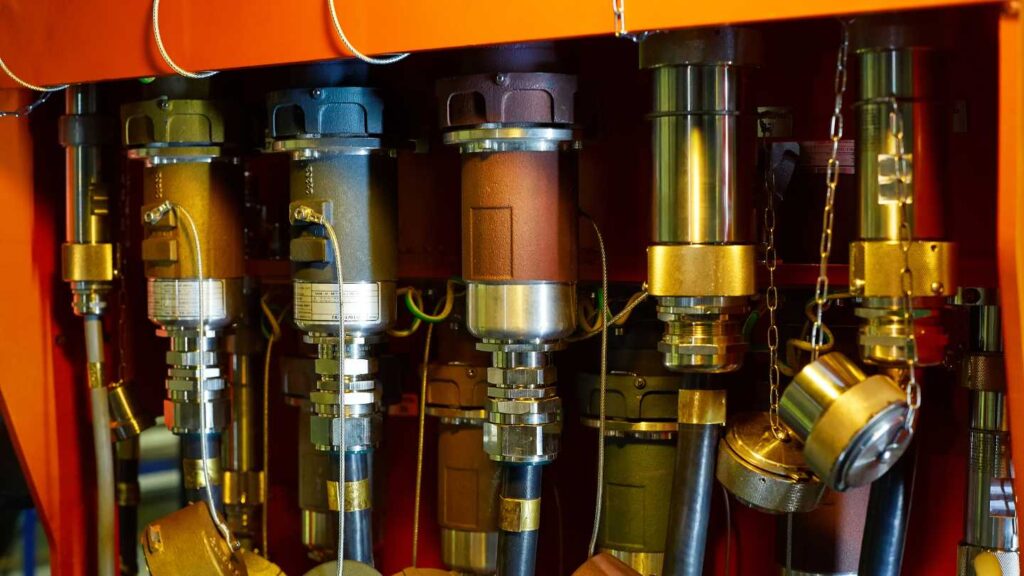
Conclusion: Invest in Regular Hydraulic Fluid Testing
Regular hydraulic fluid testing is not just a maintenance task—it’s a strategic investment in your equipment’s longevity and performance. By monitoring key fluid parameters, you can detect issues early, prevent costly failures, and ensure your hydraulic systems operate at peak efficiency.
CT Hydraulics offers expert advice, high-quality components, and reliable services to help you maintain your hydraulic systems effectively. Contact us today or visit our website to learn more about our products and services. Don’t wait for an unexpected breakdown—schedule your hydraulic fluid test today and keep your systems running smoothly for years to come.
Ensure your hydraulic systems are protected with regular fluid testing—because prevention is always better than repair.